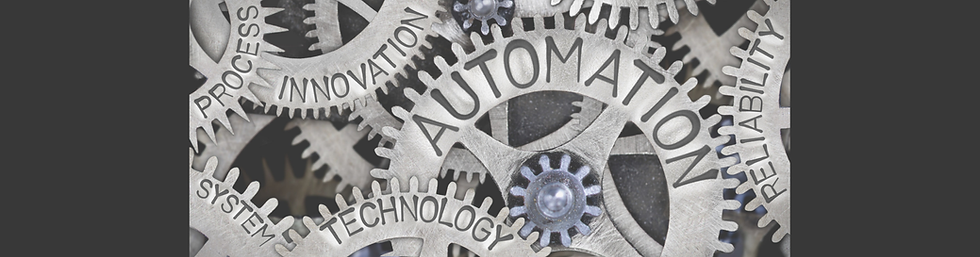
Bespoke Engineering For Industry
.png)

HCDM V21C
Classic Brought Up to Date
The Service (Engineers) Handle Cutting and Deseaming Machine is a workhorse of the ceramic tableware industry, but it has its little flaws.
​
At Cornfield Engineering we have taken all the good bits and infused it with our imaginative engineering to make it fit for the modern manufacturing wold.
​
Take a look at some of the improvements we have made and how they will enhance your production, we even offer a part exchange service so that you do not lose any valuable production time.

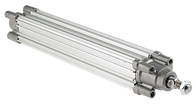
Standard Pneumatic Cylinders
The original machine used bespoke pneumatic cylinders, great for initial manufacture not so good for maintenance.
We have chosen to use only standard pneumatic cylinders allowing for good spares availability meaning easy maintenance.


Superior Drip Protection for the Up Pusher
The up pusher has always been a problem area, the gaiter breaks, fills with slurry and the cylinder fails soon afterwards.
We have reimagined the system such that there are no crevice points to cause failure and all parts are fully washable. The only wear part being a small low cost seal.

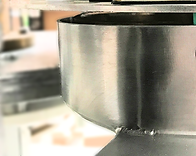
Another significant problem was the poor performance and life of the seal on the waste water bath. The tight corners and fixed position led to leakage and cracking causing drips on the part processed handles.
​
We had a light bulb moment and completely changed the shape of the bath and put in an active seal. The bath now has a single radius seal that can compensate for wear giving a high quality long life seal. This improves the quality of the final product and reduces the need for maintenance operations.

Long Life Active Seal

Reliable Flexible Controls
If you have ever tried to adjust the timing cam shaft on the machine you will appreciate this improvement.
​
We have removed the timing cam shaft and replaced it with an encoder, PLC and HMI. This means that you no longer need to make multiple adjustments to the small cams but can make the changes at will on the HMI. You can even save them to a recipe and recall them next time you make that shape. Lets also not forget that there is no longer a chain to fall off.
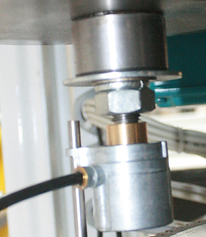
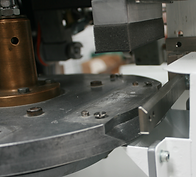
Variable Speed
When you have a difficult to process shape fine adjustment of the speed of the turntable and cutter rotor can make all the difference.
​
That is why we have equipped the machine with variable speed drives. The turntable can operate at different speeds for the index and the processing parts of the cycle and of course can be different across different products using the recipe system. Likewise the rotor can operate at different speeds during cutting and idling and across different products.
